WTS Wall Thickness System
Introduction
The Wall Thickness System (WTS) is a new real-time wall thickness measuring system designed specifically for plastic bottles and containers. The system is installed on an existing conveyor downstream of a blow molding machine for 100% product inspection. The WTS reads thicknesses of each container in desired locations and stores the results in database. The results are displayed instantly on charts providing immediate feedback information for machine operator to quickly adjust and optimize blow molder settings after changeovers and during daily production. The WTS can also be set to automatically alert operators with stack light and to reject containers that exceed specified thickness limits with an automatic air blast blow-off.

Applications
- Minimum container size: 1.0 x 1.0 x 1.5" (25 x 25 x 38 mm) (l x w x h)
- Maximum container size: 8.5 x 8.5 x 10" (216 x 216 x 254 mm) (l x w x h)
- Container shape: symmetrical, non-symmetrical
- Container material: PET, HDPE, LDPE, PC, PP
- Container transparency: transparent, semi-transparent
- Container color: Clear, Green, Blue, Amber, other
- Thickness range: 0.003 – 0.157” (0.08 – 4 mm)
- Throughput: Up to 30,000 containers per hour
Principle of Operation
An integrated trigger installed immediately before the WTS’ probes tells the system that a container is approaching the measurement station on the conveyor. The container position is tracked by the trigger and an encoder that continuously senses the speed of the conveyor. The probes are aimed to desired measurement locations, independently on each side, and each of them scan every container at a high rate resulting often in hundreds of readings from each measurement area, depending on the conveyor speed and container diameter. As the bottle moves through the station and the measurement is completed by all the probes, the WTS software then instantly calculates, stores and displays minimum, maximum and average thickness values from each measurement area. The values are compared to pre-set limits and when needed, the machine operator is alerted by the stack light. As the container position is still being tracked by the system, a bad container can be rejected by an air blast blow-off nozzle located typically immediately downstream of the WTS system. The blow-off can also be activated manually to collect product samples for Quality Control and other purposes.
The WTS system can be programmed by trained plant personnel for virtually unlimited number of different container types. The pre-set “recipe” for the desired container type is selected from the list, the probes are positioned and the system is then ready for production. The stored recipes include independent measurement location-specific parameters for thickness alarm/reject limits, measurement location, mode and probe positioning. The software enables targeting of critical areas in flat-walled and non-symmetric containers. The machine operator may also select active blow mold cavities and package type for each production run separately.
All the pertinent measurement data is stored in the SQL database. Measurement date and time, cavity number, probe number, minimum, maximum and average thicknesses, rejection status, conveyor speed, etc. for each measurement location in every container are recorded and stored. The data is used for instant real-time and run charting on WTS’ integrated touch screen monitor. The measurement data is also available for other reporting purposes whenever required at a later stage.
Reporting
The two main screens used in the system’s everyday operation are Real-Time Overview and Operational Charts. The Real-Time Overview contains a thickness X-chart for each probe/measurement location. These charts are updated in real time immediately after a container is measured and analyzed by the software. Each dot in the chart shows minimum (red), maximum (blue) and average (green) readings from the measurement area in each container. Average trend and control limits for each probe are displayed as well. In addition, the screen shows probe locations, container count, reject count, last cavity number and conveyor speed.
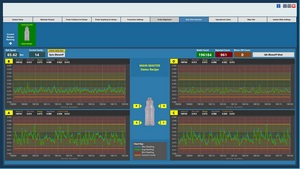
The Operational Charts enable deeper analysis of current or earlier production runs. The measurement data for each probe/measurement location can be scrolled through based on time or container count. A similar thickness X-chart as in Real-Time Overview is shown for each probe/measurement location with an additional Thickness Variance vs. Standard chart. A horizontal histogram for both charts is displayed too. Container and reject counts, minimum, maximum and average thickness results from the selected run are shown as well.
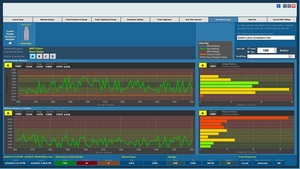
The WTS software system features Microsoft SQL Server that manages the database where all the thickness measurement results along with a variety of other pertinent data is stored. The data can be imported to Microsoft Excel or other software applications for different reporting purposes.
Expanded System for Multiple Production Lines
Production facilities with multiple blow molding lines can benefit from a cost-efficient WTS system that features a master unit that shares the PC, touch screen, application software, SQL Server, database, optional cellular connections etc. between multiple production lines. Each production line would require an individual measurement station (slave) with its own probes. Each WTS station is equipped with casters that allow easy mobility between production lines.
Connect with us
Contact us for more information
Phone (770) 633-3934
Email sales@gprllc.us